Inspection is a necessary but non-value-adding activity whose purpose is to protect the customer from poor quality. We should therefore do as little as possible, upon condition that our inspection plan meets the customer’s requirement. Inspection plans with acceptance numbers of zero (c=0) minimize the sample size, albeit at the cost of a higher producer’s risk of rejecting lots at the specified acceptable quality level (AQL).
WHY SHOULD YOU ATTEND?
This presentation will show how to define c=0 plans whose customer protection is equivalent to that of the corresponding ANSI/ASQ Z1.4 (formerly MIL-STD 105) plan.
AREA COVERED
- How to use ANSI/ASQ Z1.4, including the definition of the sampling plan based on the inspection level, acceptable quality level (AQL), and lot size.
- How to use the standard’s switching rules to move between normal, tightened, and reduced inspection where appropriate
- Understand the benefits of double and multiple inspection plans in terms of their ability to accept good lots very quickly, and reject bad ones quickly, to reduce the average sample size.
- Convert any ANSI/ASQ Z1.4 plan into a zero acceptance number (c=0) plan that provides equivalent or better protection against poor quality at the rejectable quality level (RQL). (ANSI/ASQ Z1.4 plans do not have formal RQLs, but we pretend that the nonconforming fraction for which the consumer’s risk of acceptance is 10% is the RQL). A c=0 plan has a smaller sample size than any single, double, multiple, or sequential sampling plan.
- Nothing is free in industrial statistics, though, and the cost of less inspection is a higher producer’s risk of rejecting lots at the AQL. A c=0 plan should therefore be used only when quality is far better than the specified AQL.
- Generate an operating characteristic (OC) curve that compares the protection from the c=0 plan to that of the original ANSI/ASQ Z1.4 plan to gain the customer’s agreement for the use of a c=0 plan.
Attendees will also receive an Excel spreadsheet that shows the operating characteristic (OC) curve for a c=0 plan and compares it to the original ANSI/ASQ Z1.4 plan. Attendees can replace the example’s specification with their own.
WHO WILL BENEFIT?
- Quality Managers
- Quality Inspectors
- Quality Technicians
- Quality Engineers
- Engineering Departments
This presentation will show how to define c=0 plans whose customer protection is equivalent to that of the corresponding ANSI/ASQ Z1.4 (formerly MIL-STD 105) plan.
- How to use ANSI/ASQ Z1.4, including the definition of the sampling plan based on the inspection level, acceptable quality level (AQL), and lot size.
- How to use the standard’s switching rules to move between normal, tightened, and reduced inspection where appropriate
- Understand the benefits of double and multiple inspection plans in terms of their ability to accept good lots very quickly, and reject bad ones quickly, to reduce the average sample size.
- Convert any ANSI/ASQ Z1.4 plan into a zero acceptance number (c=0) plan that provides equivalent or better protection against poor quality at the rejectable quality level (RQL). (ANSI/ASQ Z1.4 plans do not have formal RQLs, but we pretend that the nonconforming fraction for which the consumer’s risk of acceptance is 10% is the RQL). A c=0 plan has a smaller sample size than any single, double, multiple, or sequential sampling plan.
- Nothing is free in industrial statistics, though, and the cost of less inspection is a higher producer’s risk of rejecting lots at the AQL. A c=0 plan should therefore be used only when quality is far better than the specified AQL.
- Generate an operating characteristic (OC) curve that compares the protection from the c=0 plan to that of the original ANSI/ASQ Z1.4 plan to gain the customer’s agreement for the use of a c=0 plan.
Attendees will also receive an Excel spreadsheet that shows the operating characteristic (OC) curve for a c=0 plan and compares it to the original ANSI/ASQ Z1.4 plan. Attendees can replace the example’s specification with their own.
- Quality Managers
- Quality Inspectors
- Quality Technicians
- Quality Engineers
- Engineering Departments
Speaker Profile

William A. Levinson, P.E., is the principal of Levinson Productivity Systems, P.C. He is an ASQ Fellow, Certified Quality Engineer, Quality Auditor, Quality Manager, Reliability Engineer, and Six Sigma Black Belt. He is also the author of several books on quality, productivity, and management, of which the most recent is The Expanded and Annotated My Life and Work: Henry Ford’s Universal Code for World-Class Success.
Upcoming Webinars
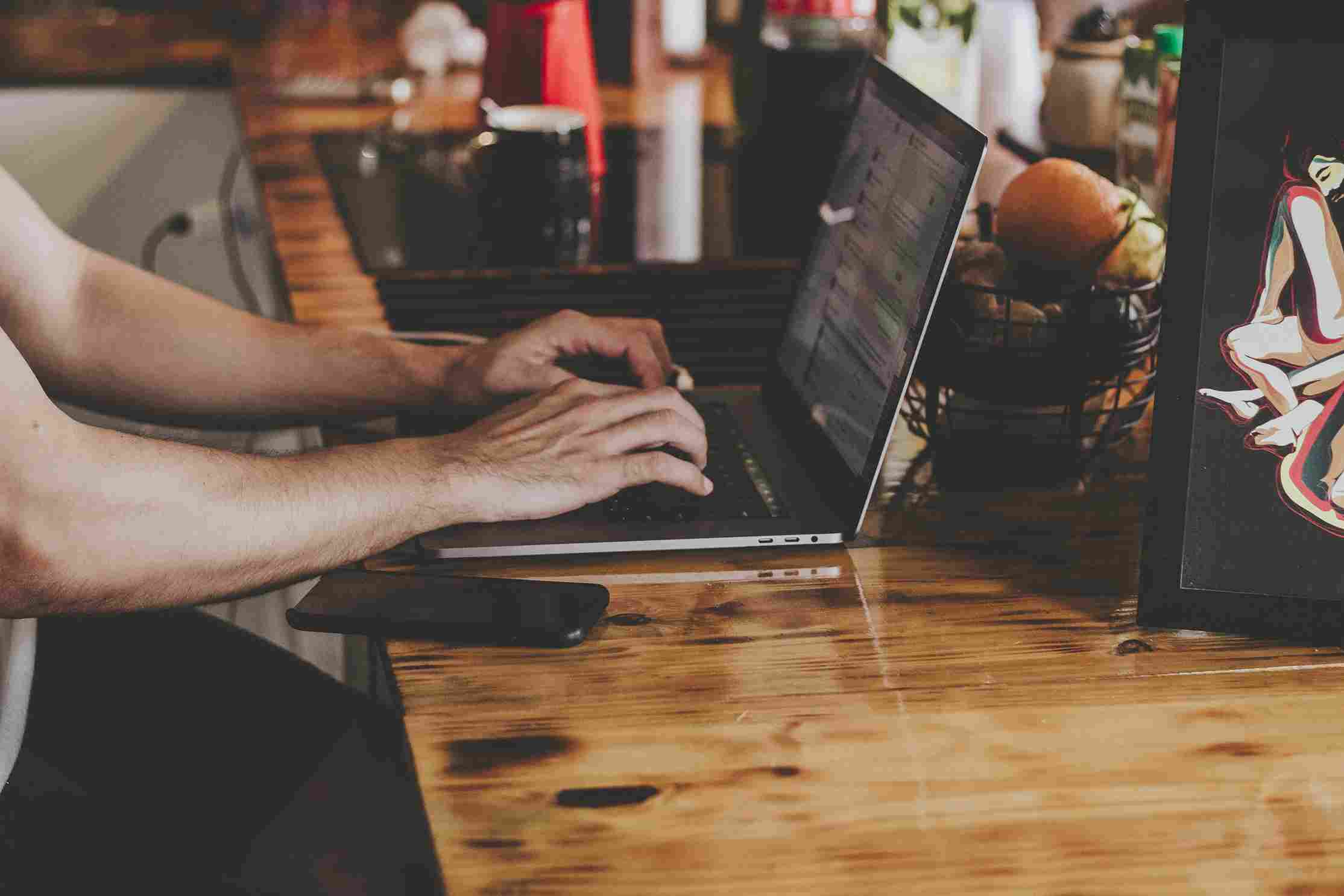
Excel - 10 Key Worksheet Functions to Skyrocket Your Produc…
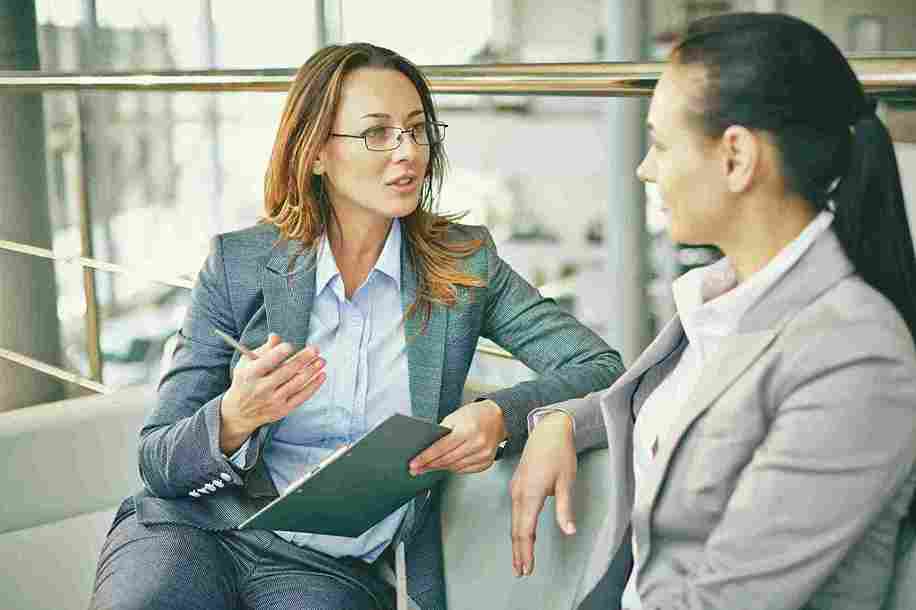
Managing Toxic Employees: Strategies For Leaders To Effecti…
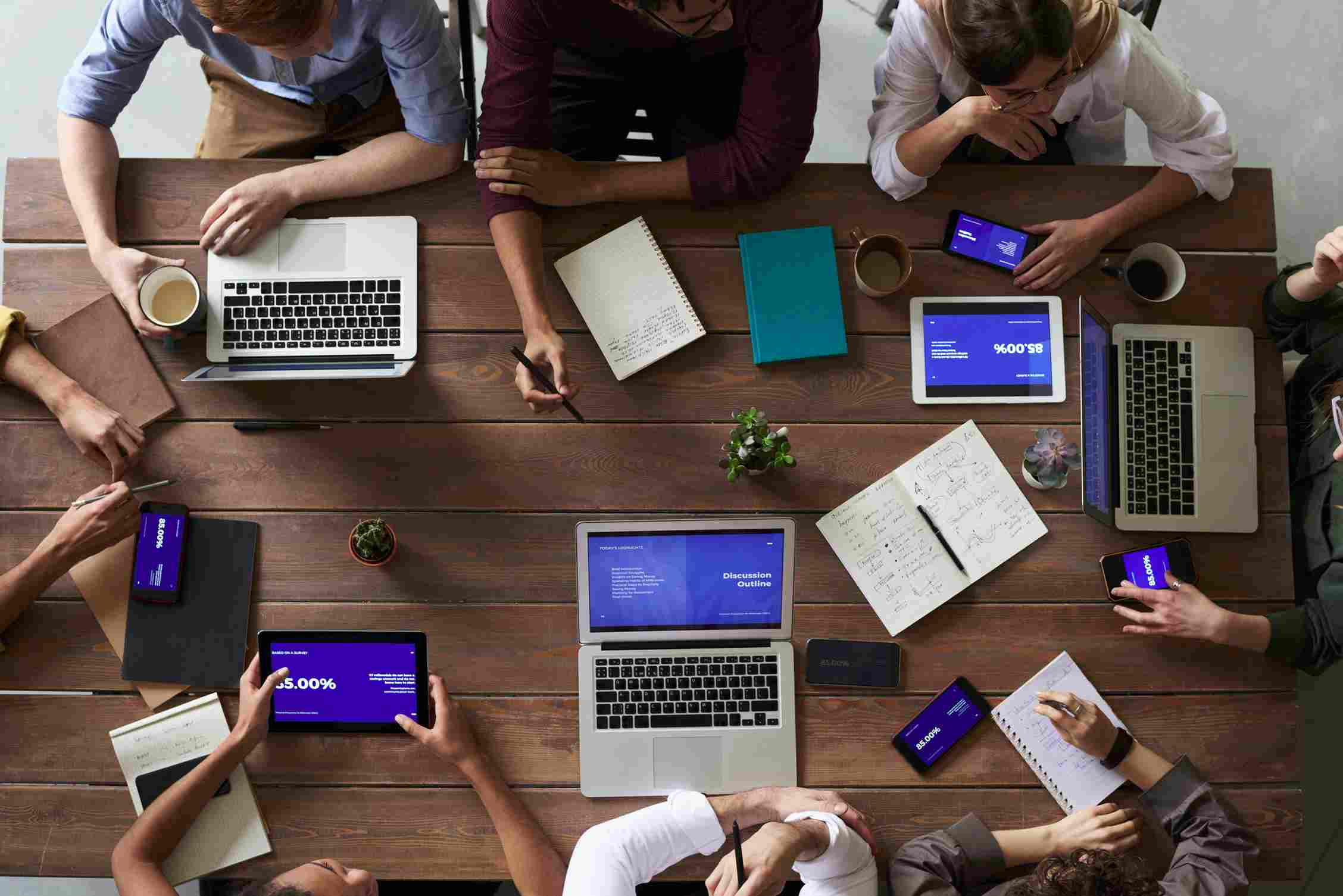
Hiring and Retaining Employees in this Crazy Economy
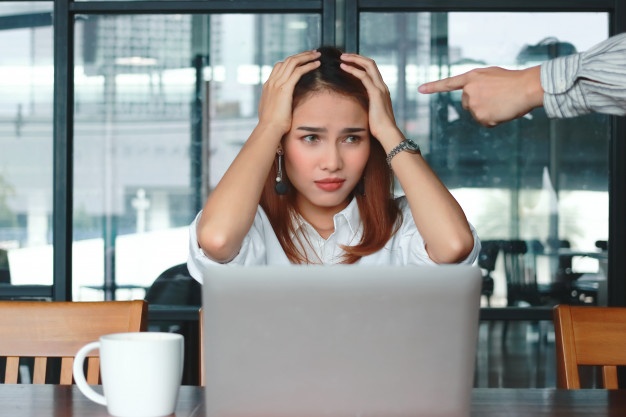
Harassment, Bullying, Gossip, Confrontational and Disruptiv…
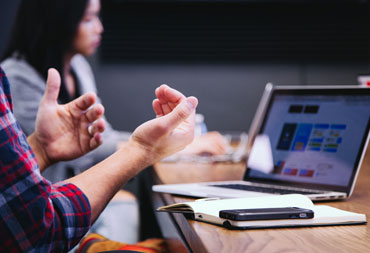
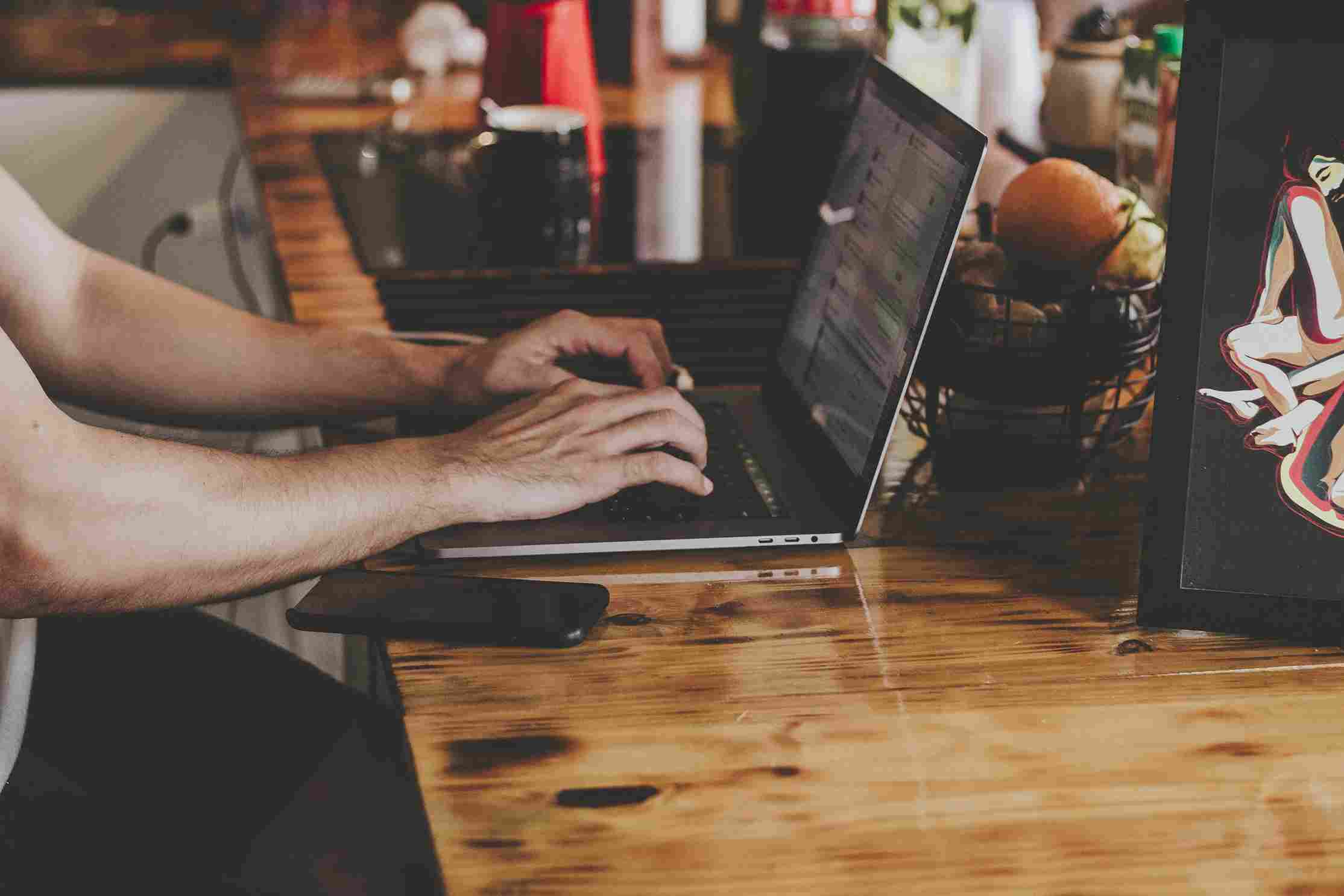
Excel Power Skills: Master Functions, Formulas, and Macros …
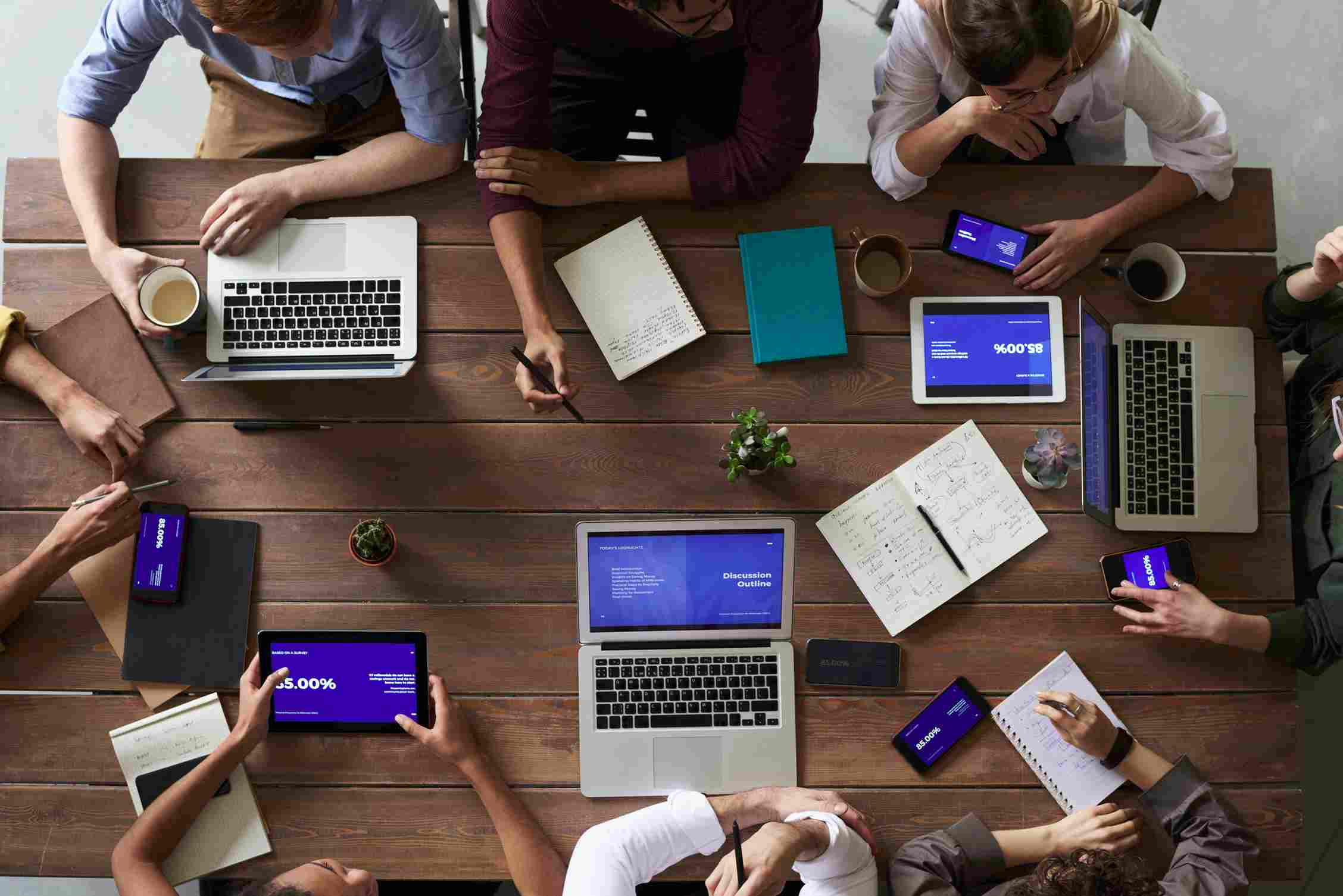
Project Management for administrative professionals
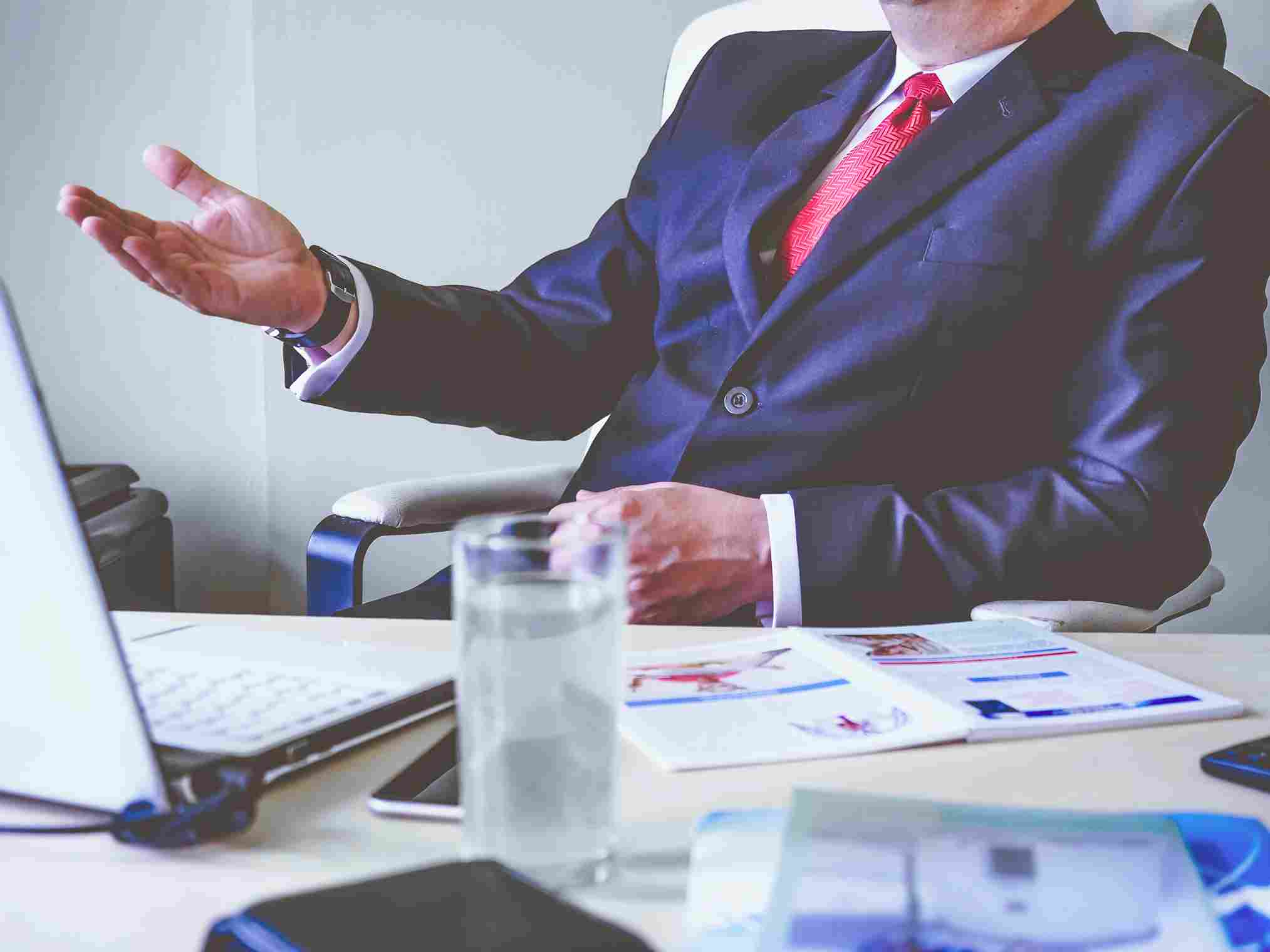
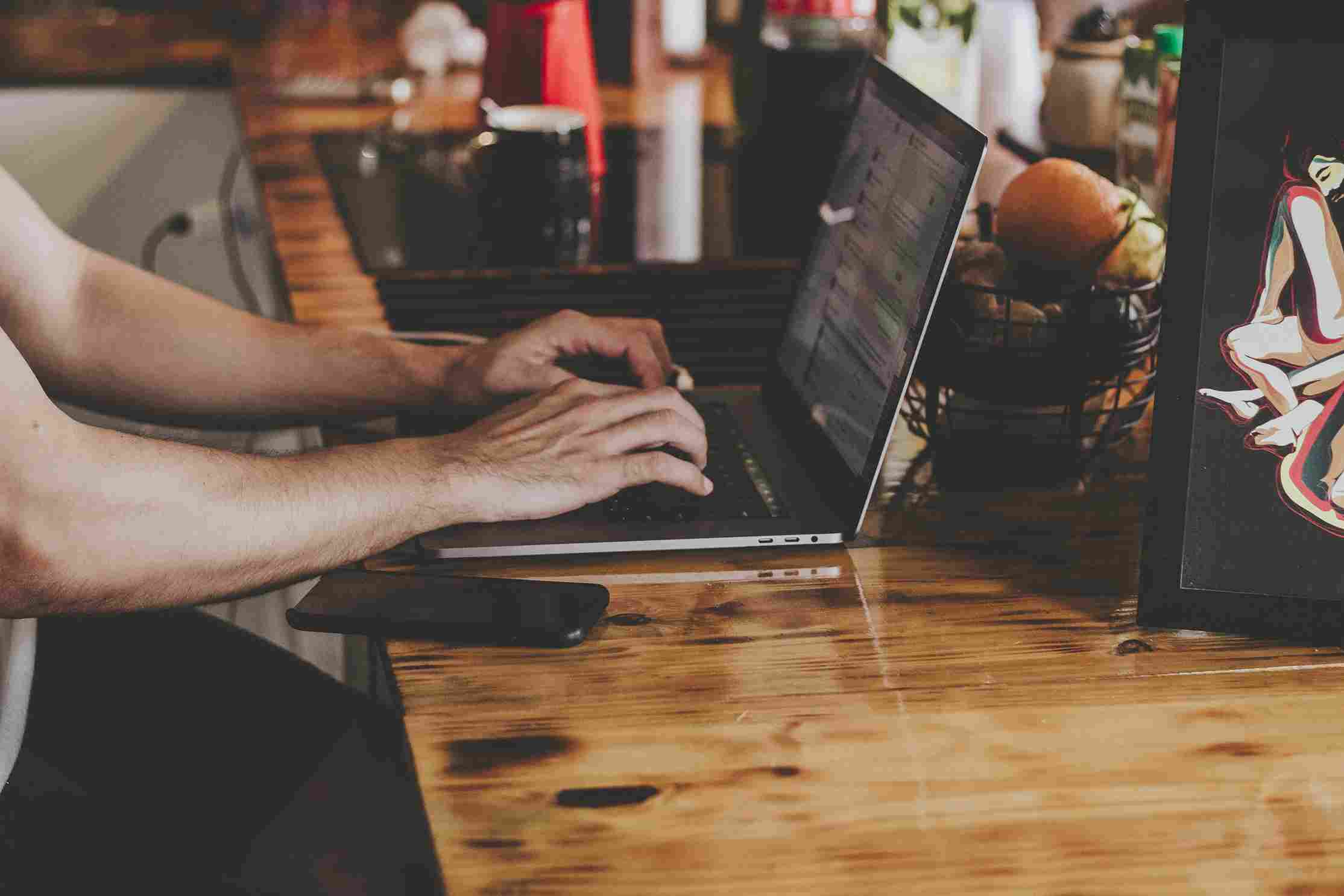
Outlook - Master your Mailbox - Inbox Hero Inbox Zero
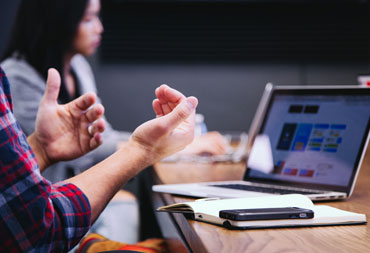
Copilot and HR: An Introduction for HR Professionals
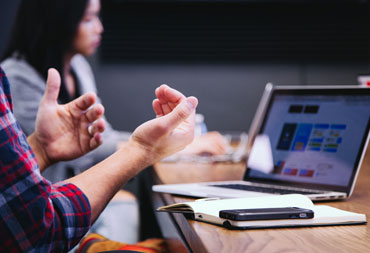

California Meal and Rest Breaks: What You Don't Know Can Co…
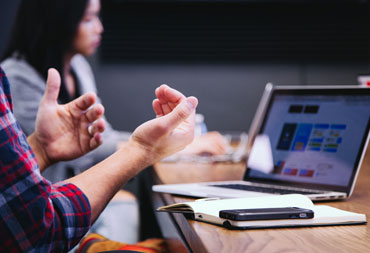
Bootcamp for New Managers and Supervisors: Develop These Es…
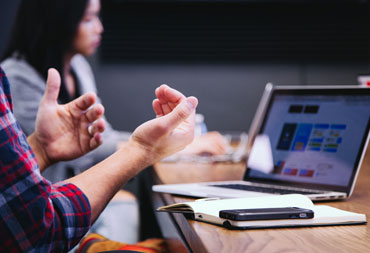
Policy Pops: Navigating DEI in the 2025 Workplace: Strategi…
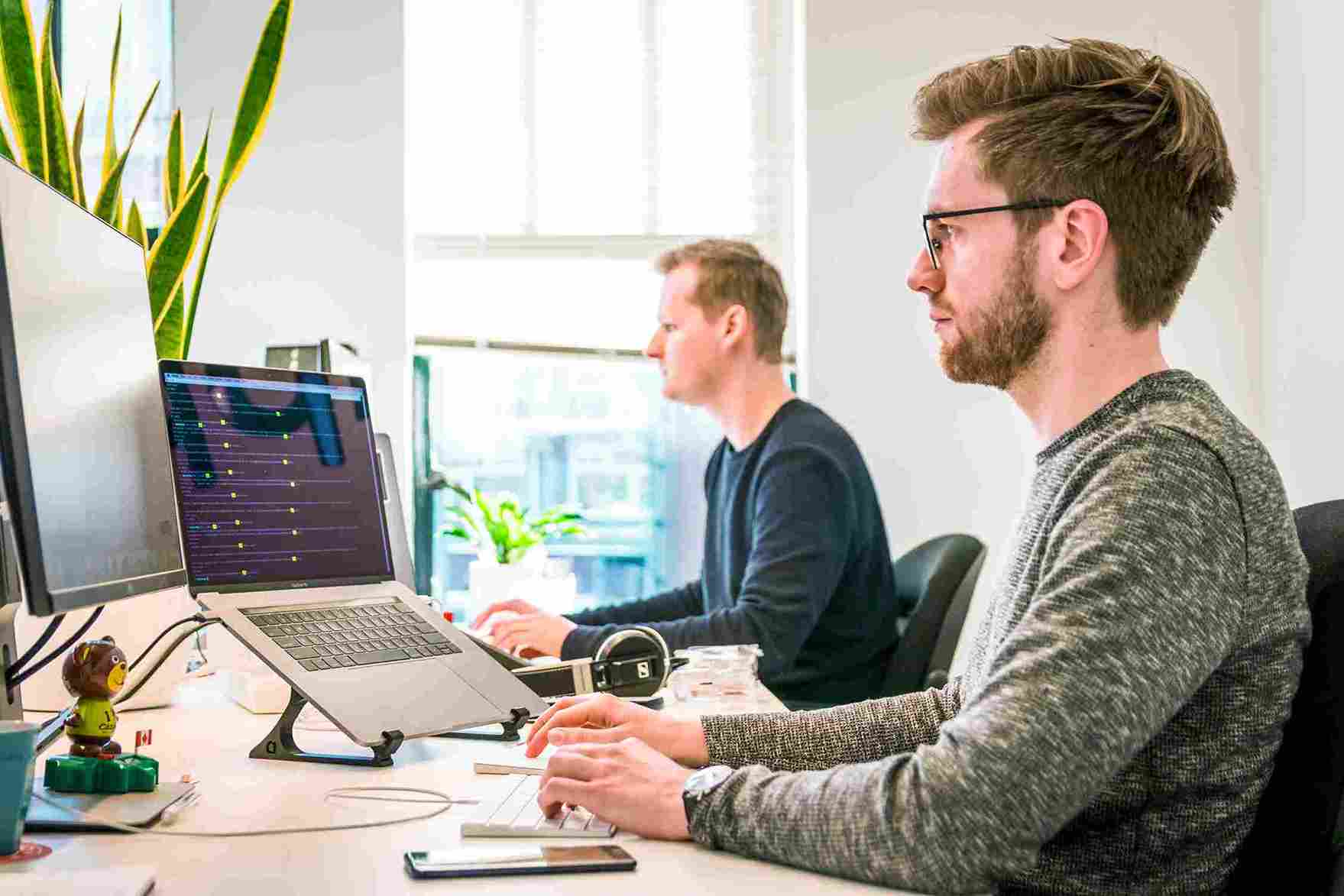
Emotional Intelligence: Mastering the Emotions of Great Lea…
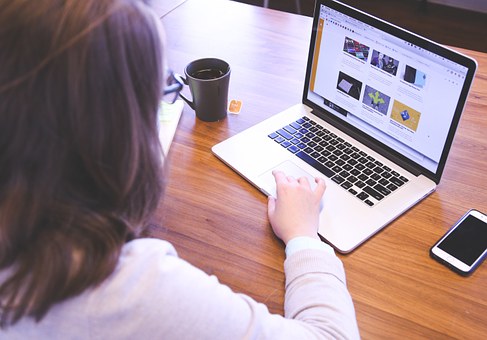
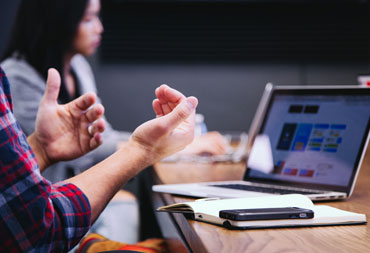
How To Conduct An Internal Harassment And Bullying Investig…
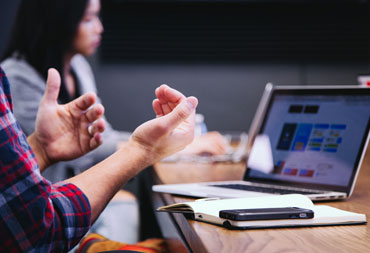
Managing Difficult Employee Conversations
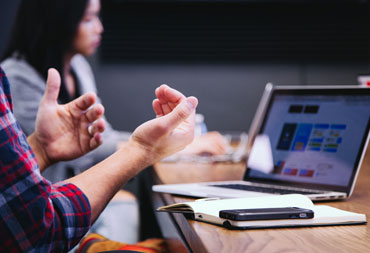
How to Manage the Legal Landmine of the FMLA, ADA and Worke…
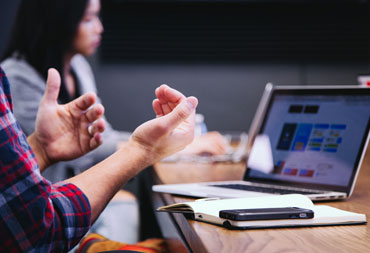
The Importance of the first 5 seconds when presenting
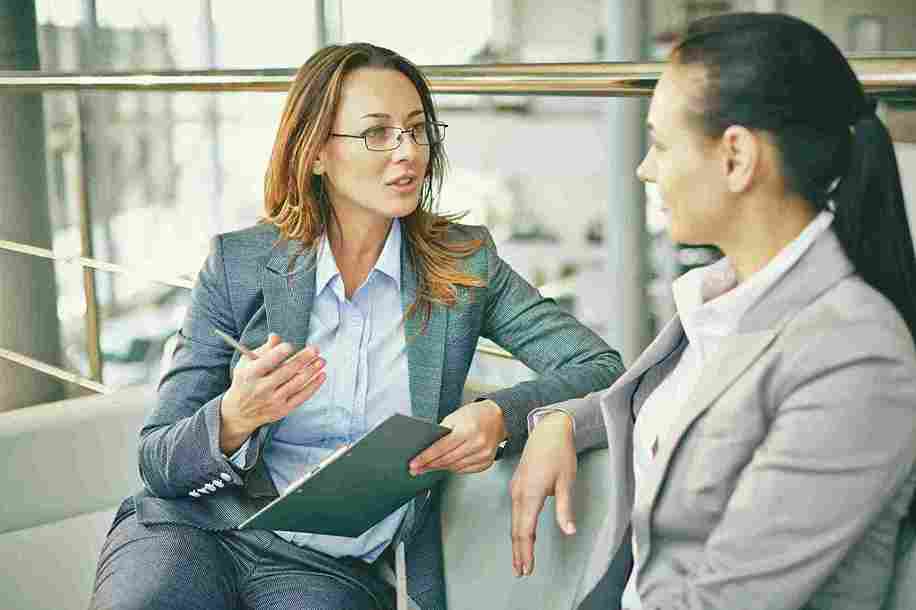
Female to Female Hostility @Workplace: All you Need to Know
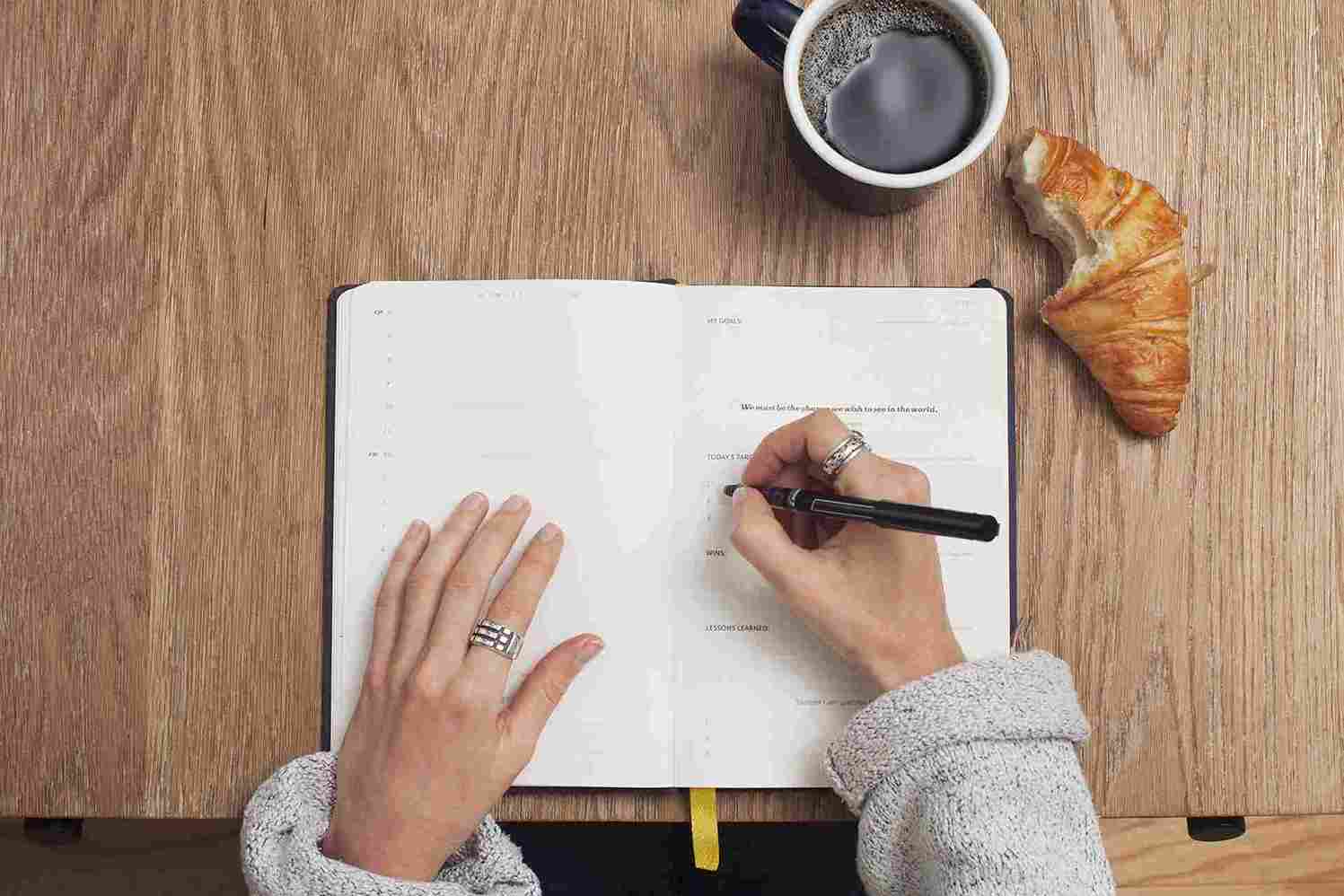
How to Write Effective Audit Observations: The Principles f…
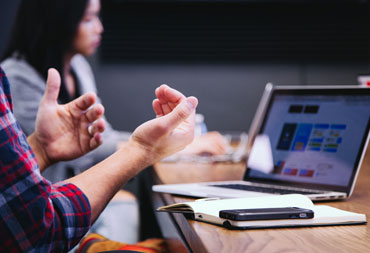
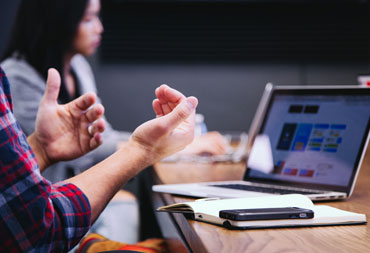
FDA Proposes Framework to Advance Credibility of AI Models